SOLDADURA POR PUNTOS DE RESISTENCIA
La soldadura por puntos de resistencia esta basada en el sistema de soldadura mas antiguo que se conoce, pero a pesar de ello tiene completa vigencia hoy en día, empleándose masivamente en la industria del automóvil, electrodomésticos de linea blanca y muebles rnetalicos, entre otras. No obstante, el método y los equipos disponibles para su aplicación han ido incorporando los avances de la técnica. Por ello, se pretende dar una visión de la situación actual de este sistema de ensamblaje en la reparación de carrocerías de automóviles, reflejando sus particularidades; métodos, equipos y recomendaciones de uso.
La soldadura por puntos es un método de soldadura por resistencia que se basa en presión y temperatura, en el que se calienta una parte de las piezas a soldar por corriente eléctrica a temperaturas próximas a la fusión y se ejerce una presión entre las mismas. Generalmente se destina a la soldadura de chapas o láminas metálicas, aplicable normalmente entre 0,5mm y 3mm de espesor.
El soldeo por puntos es el más difícil y complicado de los procedimientos de soldadura por resistencia. Los materiales bases se deben disponer solapados entre electrodos, que se encargan de aplicar secuencialmente la presión y la corriente correspondiente al ciclo produciendo uno o varios puntos de soldadura.
Éste es el sistema de soldadura que se emplea con mayor frecuencia tanto en fabricación como en reparación, debido a las ventajas que posee frente a otros sistemas de unión:
- Siempre que su ejecución se lleve a cabo de la manera correcta, se obtienen soldaduras de buena calidad y uniformes, que presentan una zona fundida homogénea, sin huecos, rechupados o grietas.
- Su manejo es sencillo, ya que la mayoría de los equipos utilizados hoy en día, tanto en fabricación como en reparación, son automáticos. Por esta razón, la calidad final ya no depende tanto de la destreza del operario, sino de la regulación de los parámetros de la máquina de acuerdo con el tipo de trabajo que se desea realizar.
- Ausencia de deformaciones y cambios en la estructura del material, debido a que la aplicación de calor es mínima y se lleva a cabo de forma muy localizada en la zona de contacto de los electrodos.
- Las superficies que se obtienen son relativamente suaves, libres de fusión superficial o huellas profundas, que hacen innecesario un repaso posterior como operación de acabado.
- No requiere material de aportación, lo cual reduce costes.
- El desmontaje de piezas unidas por puntos de resistencia es sencillo. Haciendo uso de las herramientas específicas para esta función, se realizará de forma rápida y, lo que es aún más importante, sin causar desperfectos en las piezas adyacentes.
- Es un sistema que permite restaurar la protección anticorrosiva antes de ejecutar la soldadura, mediante la aplicación de imprimaciones soldantes apropiadas.

PROCEDIMIENTO DE SOLDEO POR PUNTOS DE RESISTENCIA
Aprovechando esta energía y con una determinada presión se logra la unión. Solamente se obtienen soldaduras uniformes si las chapas a soldar están limpias, los óxidos superficiales son causa de variaciones en el tamaño y resistencia de los puntos de soldadura. Esto es especialmente cierto en el aluminio. La presencia de óxidos o suciedad puede aumentar diez veces o más la resistencia total entre los puntos de los electrodos.
La soldadura por resistencia es aplicable a casi todos los metales, excepto, zinc y plomo. Junto con la soldadura MIG-MAG son los dos procesos de soldadura en los cuales existe un mayor nivel de automatización robotizada.
El procedimiento en concreto es:
- Colocación de la pinza sobre las chapas.
- Tiempo de bajada: es el tiempo que transcurre desde que se inicia la operación de acercamiento de los electrodos hasta que comienza el paso de corriente. En este tiempo se consiguen aproximar las chapas que se van a unir para obtener una buena continuidad.
- Tiempo de soldadura: tiempo durante el cual está pasando la corriente eléctrica.
- Tiempo de mantenimiento o de forja: es el tiempo transcurrido entre el corte de la corriente y el levantamiento de los electrodos. Esta fase posterior de enfriamiento con mantenimiento de la presión garantiza el grado de resistencia y debe ser, como mínimo, igual al tiempo de soldadura.
- Separación de los electrodos.
- Colocación de las chapas o de la pinza para un nuevo punto.

OTROS ASPECTOS IMPORTANTES EN LA EJECUCIÓN DE LA SOLDADURA POR PUNTOS.
Además de las particularidades indicadas, existen otros aspectos que también hay que tener en cuenta a la hora de unir piezas por puntos de resistencia.
- Distancia entre puntos o paso.
La práctica demuestra que no es cierto que aumente la solidez del conjunto al multiplicar el número de puntos y reducir el paso entre ellos, pero si un punto se ejecuta muy próximo a otros, puede producirse una derivación de corriente por las soldaduras cercanas (efecto Shunt); de esta forma, disminuye la intensidad de corriente necesaria para la formación del nuevo punto. No tener en cuenta este factor, implica un consumo excesivo de energía eléctrica, ya que, además de la corriente útil de soldadura, se está proporcionando a las pieza una corriente adicional, que se pierde a través de los puntos próximos.
- Distancia al borde o recubrimiento.
La distancia al borde o "recubrimiento" es la longitud medida desde el centro de la soldadura al borde de la pieza.
Un recubrimiento insuficientepuede dar lugar a:
-Expulsión de material fundido por la junta, debilitando la soldadura.
-Deformaciones en los bordes de las piezas, debido a la presión ejercida por los electrodos.
-Deterioro de los electrodos, que se ensucian con gran facilidad.
- Obtención de puntos sin marcar la cara vista.
Al ejecutar un punto de soldadura, quedará visible sobre la pieza una pequeña marca o "lenteja", debido a la presión de los electrodos. Sin embargo, existen zonas donde esta marca no puede estar visible, como por ejemplo el panel de una puerta soldado a su armazón. En tal caso, para evitar la marca por la cara vista, se interpone entre ésta y el electrodo correspondiente una placa de cobre. Puede servir una placa empleada como masa en muchas máquinas de soldadura.

- Control de calidad.
Un especialista puede reconocer la calidad del punto de soldadura por su color, que debería estar entre azul oscuro y azul violeta, con el centro blanco.
La mejor forma de evaluar la calidad de un punto es proceder a su rotura. Si se produce un arrancamiento del material base, el punto está bien realizado; si se desprende reventado, no se ha efectuado adecuadamente el trabajo. Para ello, bastará con soldar unas probetas de chapa, de igual espesor y características que las de la chapa que hay que soldar, y proceder después a su rotura. Esta prueba es muy útil para una primera regulación del equipo cuando aún no se está familiarizado con él.
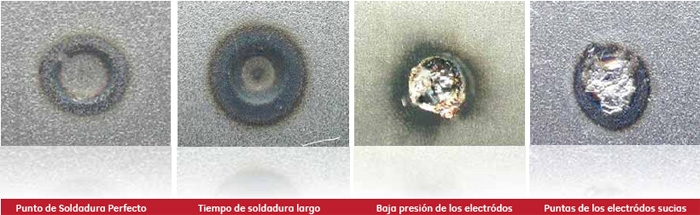
SOLDEO POR PUNTOS DE RESISTENCIA A UNA CARA
La soldadura con un sólo electrodo o por empuje se realiza aplicando un electrodo a una chapa y una masa de superficie amplia en la otra. La masa debe fijarse en las próximidades inmediatas al punto de soldadura y en la chapa donde no se aplica el electrodo. Los puntos por empuje son de escasa resistencia, dado que la chapa se abomba hacia afuera al calentarse y el material superior se une al inferior en un área muy reducida. La experiencia demuestra que estos puntos carecen muchas veces de la resistencia suficiente al no poder alcanzarse la presión de apriete requerida, por lo que es preferible sustituirlos por soldadura MIG a tapón.
Este tipo de soldadura se realiza con un solo electrodo y se realiza de la siguiente manera:
- Se realiza por empuje sobre la chapa y masa proxima al punto de soldadura.
- Es de dificil ejecución, carecen de resistencia suficiente, es preferible sustituirlo por solddura MIG a tapon.
EQUIPO DE SOLDADURA POR PUNTOS DE RESISTENCIA MULTIFUNCIÓN
Independientemente de la estructura, tamaño y tipo del equipo, todas las máquinas están diseñadas de modo que puedan suministrar a la pieza los parámetros indicados anteriormente; por ello están dotadas de los siguientes elementos básicos:
- Un sistema de puesta bajo presión de las piezas que hay que unir, que proporcionará a los electrodos una fuerza fácilmente regulable. Puede ser de accionamiento mecánico, hidraúlico o neumático. Es el responsable del apriete de las piezas, modificando en cierta medida la resistencia de contacto y, sobre todo, de llevar a cabo la forja de la soldadura, al ser capaz de mantener el esfuerzo sobre las piezas, incluso después del corte de la corriente.
- Un transformador eléctrico, cuya misión es transformar la tensión e intensidad de la corriente alterna de la red. De este modo, se consigue en la pinza una intensidad de varios miles de amperios.
- Un sistema de corte y temporización capaz de suministrar la energía deseada en el espacio de tiempo preciso.
- El cabezal o pinza de soldadura está conectado a la unidad de alimentación mediante cables flexibles de una longitud determinada. El operario soporta este elemento durante la ejecución del trabajo. Su accionamiento suele efectuarse mediante un cilindro neumático que lleva incorporado, y que es puesto en funcionamiento por la electroválvula mandada por el pulsador eléctrico. Este tipo de accionamientos se emplea cuando los esfuerzos requeridos no son muy importantes.
- Se necesita una tensión de red estable para un correcto funcionamiento.
- La presión del aire de alimentación para la pinza se halla alrededor de 6 bares.
- Si se emplean alargadores de alimentación, han de tener la sección suficiente.
- No se deben forzar las conexiones.
- Es preciso soplar con aire seco el interior de la máquina para eliminar los depósitos de polvo.
- Hay que tener la precaución de no tirar de los cables de conexión o soldadura para mover el equipo.
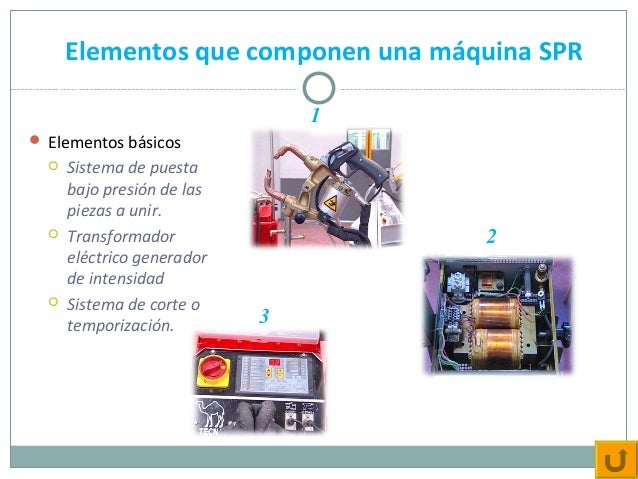
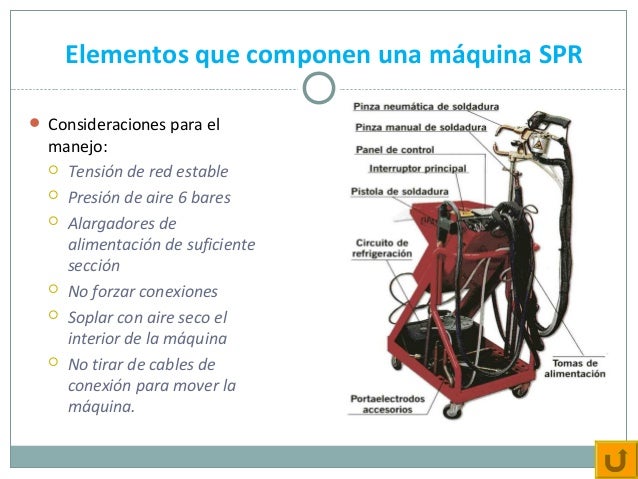
TRATAMIENTO TÉRMICO DE LAS DEFORMACIONES CONCENTRADAS
este tipo de tratamiento se utiliza para devolver un material a su forma "original", el cual con anterioridad a sufrido un recogimiento, esto se ocasiona normalmente por un golpe, para devolver el material deformado a su forma utilizamos el calor y la presión. El calor y la presión se aplicara en la zona del material que este recogido es allí donde se concentran las tensiones del material, de esta manera al aplicar el calor en este punto las tensiones se van liberando, esto permite ir moldeando la deformación para conseguir que la pieza vuelva a su forma original, aunque esto no se consigue totalmente, y ademas dependiendo de que zonas del material o pieza que reparemos sea el recogimiento nos costara mas o menos, es allí cuando tenemos que valorar si es rentable reparar dicho golpe o sustituir la pieza.
TRATAMIENTO TÉRMICO DE LAS DEFORMACIONES EXTENDIDAS
Este tratamiento es utilizado también para devolver un golpe o deformación a su forma original o intentar dejarlo lo mas parecido a su forma original, por que ya sabéis que una material o pieza que haya sufrido una deformación difícilmente vuelve a su forma original, a diferencia de la anterior en este tratamiento intentaremos recoger el material ya que la deformación que a sufrido es de estiramiento esto quiere decir que el tratamiento se debe aplicar en los bordes de la deformación y no en el centro que seria el caso anterior, sabiendo esto aplicamos el calor y presion en la zona deformada y asi podemos devolver al material a su forma "original".
USO DEL EQUIPO MULTIFUNCIÓN PARA EXTRACCIÓN DE GOLPES
Este apartado lo explicare punto por punto desde lo que se tiene que hacer inicialmente para la extracion de un golpe de la siguente manera:
- Primero se analiza el daño, para realizar o una sustitución parcial o una reparación.
- Una vez decidida la reparación, se lija la zona dañada hasta que quede desnuda mediante el clean´n strip.
- Colocar el cable de masa lo mas cercano posible a la superficie a reparar.
- El tipo de elementos soldados debe ir en función del golpe y esfuerzo.
- La separación de los elementos soldados no debe ser muy grande para que se pueda extraer poco a poco.
- Soldar el numero de elementos necesarios y acoplar el martillo de inercia para tirar elemento por elemento, o acoplando un pasador y una cadena a dos arandelas para tirar de una zona mas amplia a la vez, acoplar el martillo de inercia y lanzamos la masa que se encuentra en su eje hacia el exterior para traer la chapa a su forma original.
- La fuerza que se aplicara va en función de la fuerza ejercida sobre la masa de inercia, y de la superficie en contacto. Reparación de deformaciones en zonas de la carrocería con difícil acceso o zonas cerrad.
- A la vez que estamos tirando de la chapa, debemos golpear con un martillo, las costillas de la chapa para liberar tensiones y facilitar el ajuste.
- Una vez restablecido el hundimiento de la chapa, se quitan los elementos soldados girándolos sobre si mismos.
- Después usamos la lima de carrocero para verificar el estado de la superficie y eliminar los restos de las arandelas.
- Esta maquinaria y técnicas no son suficientes para la reparación de un daño, necesitara material de relleno para poder pasar a la operación final de pintado.
Precauciones:
- Desembornar la batería para no dañar los dispositivos electrónicos del vehículo a consecuencia del campo magnético generado.
- Debido a la alta inducción, no es aconsejable que personas con marcapasos se acerquen mientras esta en uso.
- No es recomendable acercar relojes de cuarzo o tarjetas magnéticas mientras esta en uso.
- Antes de soldar es necesario regular la intensidad y el tiempo de operación en una chapa con las mismas características que la chapa a reparar.
- Tener mucha precaución a la hora de quitar los elementos soldados para no arrancar el material.
- Mientras se esta usando el equipo es necesario usar guantes y gafas.
- No usar el equipo en zonas donde haya concentrados gases inflamables.
Aquí os mostramos un vídeo de una reparación de un golpe con la maquina multifunción pero en este caso soldando arandelas.
SOLDEO DE ROSCAS, SETAS Y OTROS
ELEMENTOS DE FIJACIÓN DE AMOVIBLES
Es otra actividad que nos permite realizar este equipo en este caso con roscas, setas. ¿con que fin ? la finalidad de esto es poder fijar elementos amovibles al chasis, ¿como? soldando las roscas o setas al chasis para así poder fijar los elementos amovibles que deseemos fijar, en resumen estos elementos de fijación parea que nos entiendan actúan como grapas que eso lo que mas se puede ver en su mayoría en la carrocería del vehículo.
Esto ha sido todo por hoy espero que esta entrada os sea de mucha ayuda, en resumen es una maquina con el cual puedes realizar distintas funciones dependiendo del el trabajo que quierais realizar.
Un saludo y hasta pronto...
Esto ha sido todo por hoy espero que esta entrada os sea de mucha ayuda, en resumen es una maquina con el cual puedes realizar distintas funciones dependiendo del el trabajo que quierais realizar.
Un saludo y hasta pronto...
buenos dias si estan en la capacidad de enviarme fotos de puntos de soldadura defectusos que los necesito para mi tesis.
ResponderEliminaratt
Franklin Sanchez Gracias y feliz dia .